Gamekeeper turned poacher
Considerations for before, during and after
an inspection
October 2022
Many of you might know me as an MHRA Senior GDP inspector, well not anymore. I left the MHRA in January 2022 to join SeerPharmaUK as a trainer and consultant. Am I really a ‘gamekeeper’ turned ‘poacher’? I shall leave you to decide. What I do want to do is help you understand the best way to approach an MHRA inspection – to get the most out of it, to demonstrate what you do well and, most of all, to demonstrate a commitment to public safety.
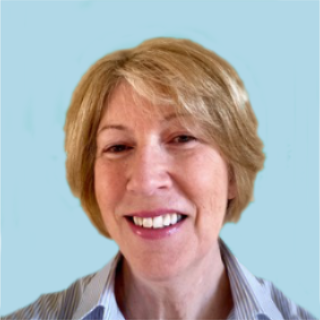
Gaynor Brummit
Director and Senior Consultant, SeerPharma UK
Many of you might know me as an MHRA Senior GDP inspector, well not anymore. I left the MHRA in January 2022 to join SeerPharmaUK as a trainer and consultant. Am I really a ‘gamekeeper’ turned ‘poacher’? I shall leave you to decide. What I do want to do is help you understand the best way to approach an MHRA inspection – to get the most out of it, to demonstrate what you do well and, most of all, to demonstrate a commitment to public safety.
You receive the MHRA letter informing you of an inspection date…. What now?
Preparing for the day when an inspector attends the site can be daunting for all staff, not just the Responsible Person or Licence Holder.
I have heard so often that a company works on an ‘audit-ready’ basis.
So, what is an ‘audit-ready’ basis? It means using your quality tools to see how well your systems, processes and documentation are working and to assess and influence quality in your organisation. It helps you identify the gaps before an inspector finds them; however when you receive the MHRA notification you are likely to feel quite anxious and wonder if all the hard work you continually put in will adequately fulfil the requirements of an inspector.
How best to prepare
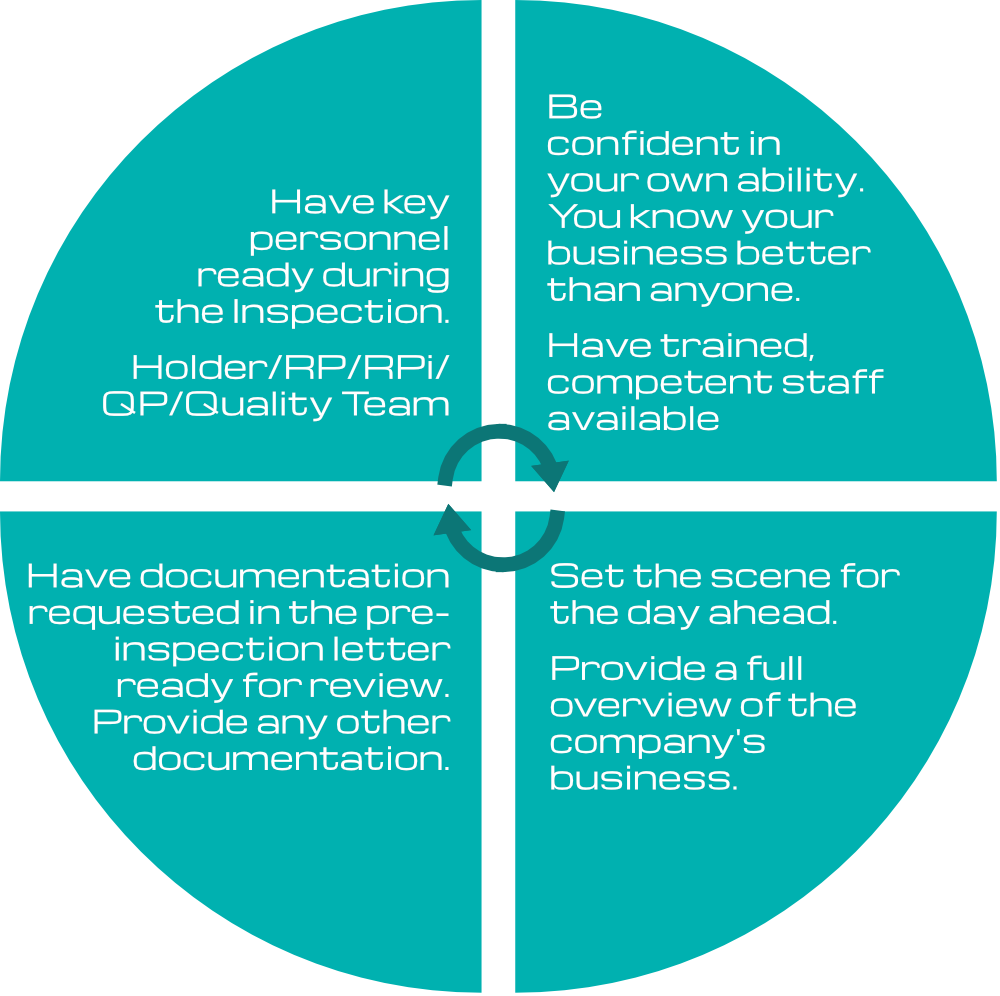
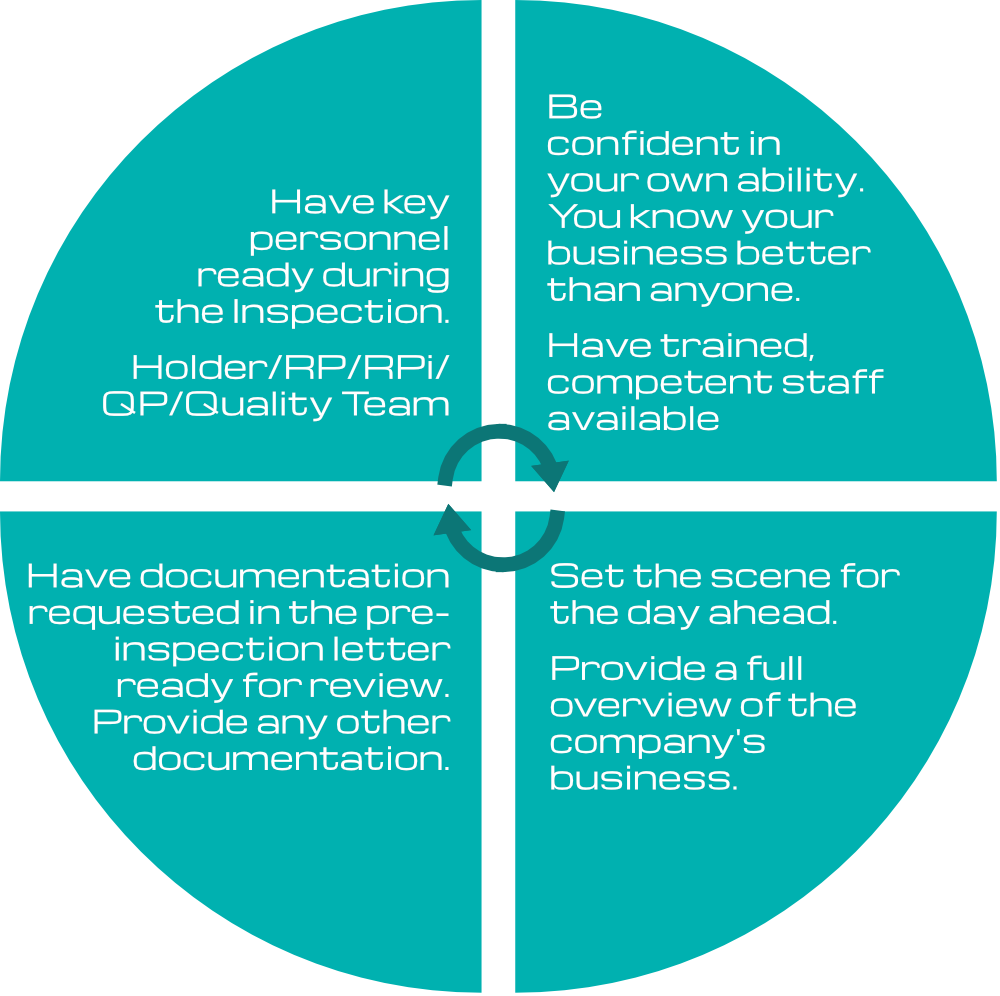
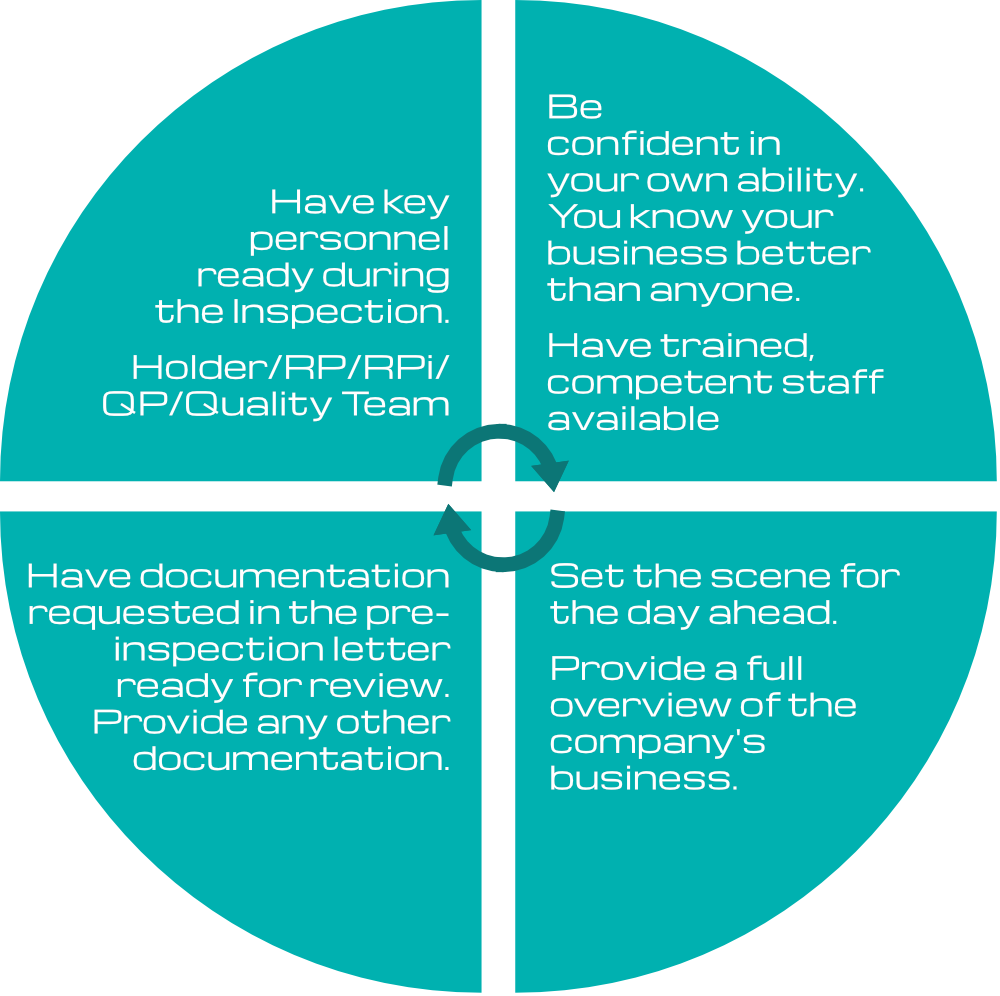
Interpreting what the MHRA inspector requires is not always an easy task. For example, what the pharmaceutical professional sees as suitable may not always correspond with what the inspector sees as suitable. This can often be confusing and daunting, particularly when a significant amount of work has already been put into writing and implementing the QMS, training and other key quality processes.
Interpreting questions and what the expected answer should be can sometimes be confusing. If there is ambiguity, ask the inspector to clarify the question, or ask them to explain it differently. This is very important, and indeed, you must ask for clarification if you do not fully understand what the inspector is requesting.
- Be honest and open
- Show what the risks are to your supply chain
- What current control measures are in place?
- Define processes and procedures in the quality management system
- Ensure staff are fully trained (ongoing) and competency training conducted
The inspector is attending to ensure you are complying with your regulatory obligation in protecting patient safety and ensuring product quality is maintained throughout the supply chain. Remember they are not there to advise or recommend.
Both the RP and the inspector have a common purpose and that is to protect patient safety and maintain product quality.
What not to ask an inspector
Am I doing it right?
Can you advise me?
Is there sufficient/adequate information in my procedures?
The inspector needs to feel confident that you understand your business model and can demonstrate your understanding of the regulations and GDP is carried out effectively. You will be expected to know you have identified, accessed, mitigated, and communicated risks. Demonstrating RP full oversight, understanding and control is fundamental in providing the inspector with assurances these obligations are being fulfilled.
What did I see as an inspector?
As an inspector, I was often incredibly impressed by the hard work and commitment of RPs, licence holders and their teams. However, all too often, companies can get bogged down in the desire to create systems that can be over-complicated. This includes producing risk assessments that fail to consider causal factors, written procedures that did not reflect the business model or work instructions that didn’t link to the correct procedure. Creating complex systems can be challenging to implement and difficult for staff to be engaged with, particularly when faced with operational factors that can impact on the day job, such as system failures, vehicle breakdown, inclement weather, shortages of medicines, increased stock holding, staff shortages etc etc.
Many RPs are extremely conscientious and want to ensure patient safety and product quality is at the forefront of the business ethos and strive in their role to ensure compliance is controlled and maintained and staff have a thorough understanding of their own roles. Having processes and systems that are overly complex can sometimes be more detrimental to providing assurances to the regulator that complete control is in place and that staff fully understand what is expected of them. Failure to recognise this could have an impact on the organisation’s outcome of an inspection.
So how can you simplify things?
Take a step back and ask yourself, what skillset do we have in our organisation? What benefits can we draw from identifying other areas of expertise in our existing team? For example, when I first became an inspector with the MHRA, I was also qualified in Health & Safety. The skills acquired in my previous employment allowed me to understand risk management and its underlying principles. This provided me with the opportunity to use this knowledge in my role as an inspector, albeit there were other areas of being an inspector where I had to undergo a significant amount of training.
One of the first things to do is identify what technical knowledge your staff have. Overlooking fundamental skillsets in your own organisation may mean your greatest asset is sitting right there and you are unaware!
Ask staff what they think. Is this operating procedure too ambiguous? Are we doing what the work instruction tells us to do? Can we use pictorial training methods alongside written processes? Are we working efficiently and effectively? As an RP, have you considered bouncing ideas off other RPs who you might have met during training?
Knowledge is gained in several ways.
School, college, university, carrying out your daily role, training sessions, listening to webinars, attending seminars. We often overlook the type of training we attend and forget to record it or, when we attend such events, we forget to disseminate it to those who would benefit within the business. Information sharing is vital not only to promoting and safeguarding medicinal product, but it also empowers and increases team morale and provides colleagues with a sense of responsibility.
From regulatory inspector to director
The transition from an MHRA regulatory inspector to a Director of SeerPharmaUK and a trainer in the training team is providing me with the opportunity to work in an environment with skilled and talented individuals who share the same passion – helping those who want to get it right and sharing the wealth of knowledge from 25 years working in industry and as a senior regulatory inspector.
Ask advice of people who know
SeerPharmaUK can provide guidance, encouragement and training. We can harness your existing knowledge, develop it to maximise your understanding of regulatory requirements and provide guidance on the expectations of the inspector. Simply having a chat sometimes helps to sort out ambiguity.
Trainers/consultants can provide a useful distance from the challenges of your business; they are not emotionally invested in operations in the same way that business owners are, and they can more easily identify and address challenges, whether the issue is implementing a new quality system or clarifying regulatory requirements.
A consultation with us can afford the freedom to bring knowledge and experience to the table, to be impartial yet observational (a fresh pair of eyes), have an open discussion on perhaps some of the weaker areas of the business and identify the stronger areas.
Sharing information through training is fundamental to all stakeholders. Many companies want to get it right and many do. However, some need that extra advice, guidance, training, and a suitable strategy to gain the recognition they so clearly deserve.
Remember, the inspector wants the same as you; both of you are working towards the same outcome.
The SeerPharma UK Team – What makes us different?
The diversity of the directors in the SeerPharmaUK team is unique. My SeerPharmaUK colleagues and I have met a lot of people through our interactions and networking.
We have an extensive pool of skills with a breadth of experience in industry, regulatory, training and consultancy and we can help support you.
We have had the unique opportunity of seeing this from both sides of the fence, which has been enlightening, interesting and insightful. We see some very high industry standards, but we also see a lot of RPs working in isolation- something I often didn’t see as an inspector. When working in isolation, it can be difficult to assess if you’re on the right track or fully complying with your duties, wanting to get it right, but not confidently knowing if you are. We have the knowledge & skillset at our fingertips and can provide the help and guidance to confirm you are on the right path. Considering my own industry experience, I wish there had been an organisation such as SeerPharmaUK out there to help us.
Do I feel like gamekeeper turned poacher? No I don’t. I believe we can all work together to achieve the same outcome and good training, guidance and an ear to listen can make all the difference.
So, in anticipating an inspection, preparation is key. Taking time to consider what training may be required well before the MHRA letter drops through the door, will lessen the impact, and make the inspection a more relaxed experience. The SeerPharmaUK team are here to help you.
If you would like a chat, please contact us.
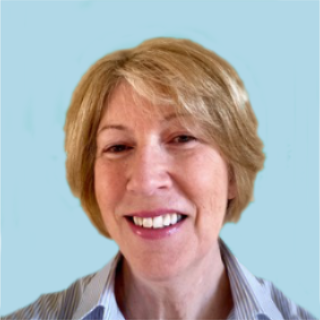
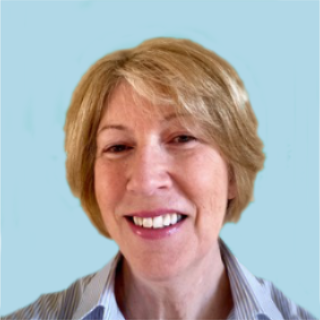
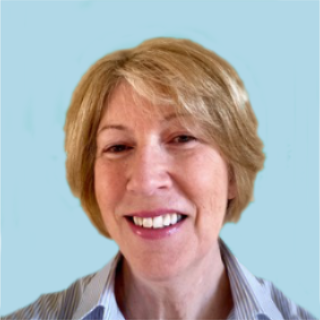
Gaynor Brummit
Director and Senior Consultant, SeerPharma UK
Many of you might know me as an MHRA Senior GDP inspector, well not anymore. I left the MHRA in January 2022 to join SeerPharmaUK as a trainer and consultant. Am I really a ‘gamekeeper’ turned ‘poacher’? I shall leave you to decide. What I do want to do is help you understand the best way to approach an MHRA inspection – to get the most out of it, to demonstrate what you do well and, most of all, to demonstrate a commitment to public safety.
You receive the MHRA letter informing you of an inspection date…. What now?
Preparing for the day when an inspector attends the site can be daunting for all staff, not just the Responsible Person or Licence Holder.
I have heard so often that a company works on an ‘audit-ready’ basis.
So, what is an ‘audit-ready’ basis? It means using your quality tools to see how well your systems, processes and documentation are working and to assess and influence quality in your organisation. It helps you identify the gaps before an inspector finds them; however when you receive the MHRA notification you are likely to feel quite anxious and wonder if all the hard work you continually put in will adequately fulfil the requirements of an inspector.
How best to prepare
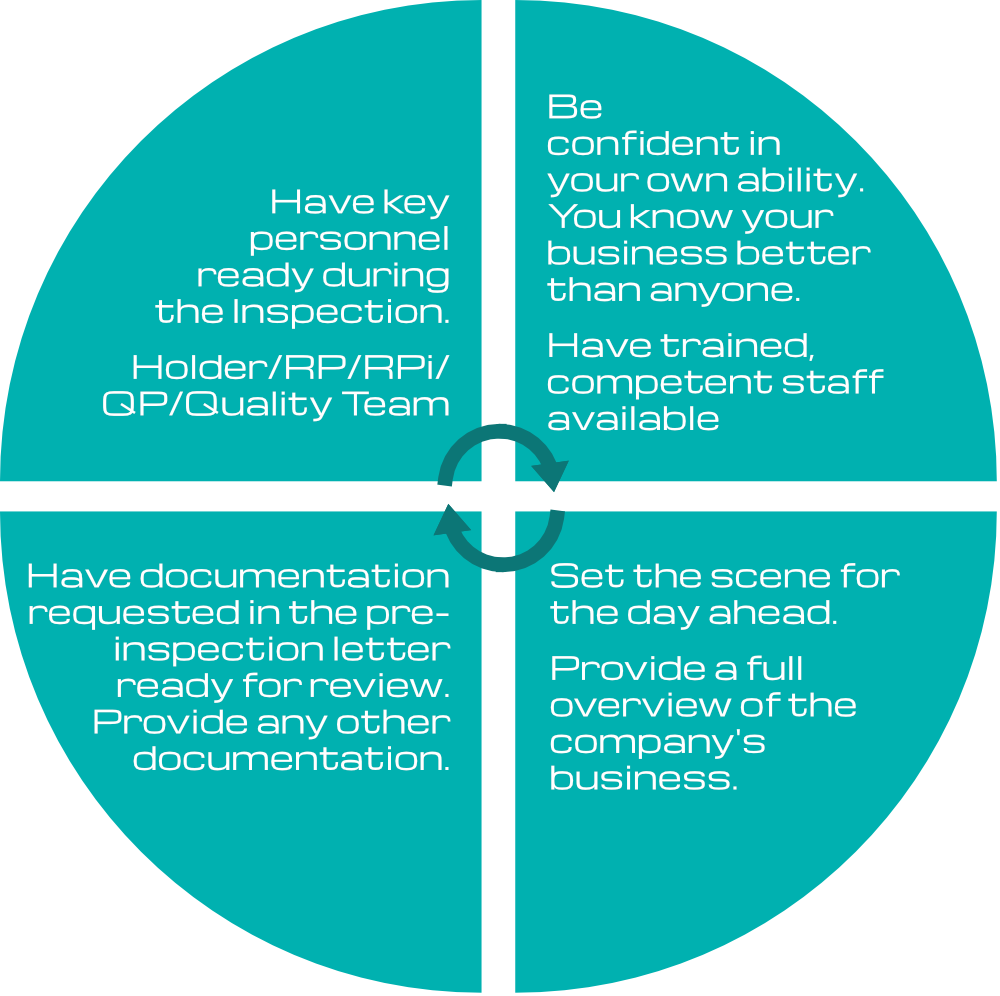
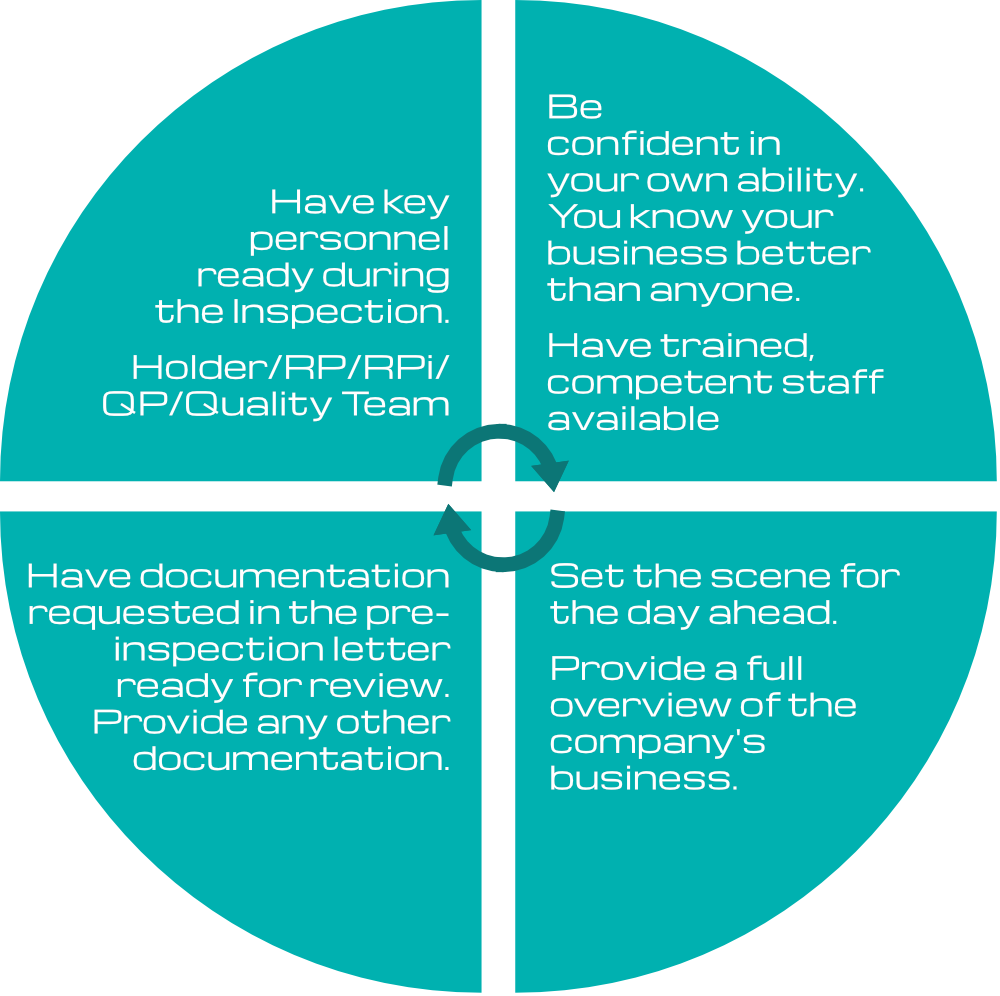
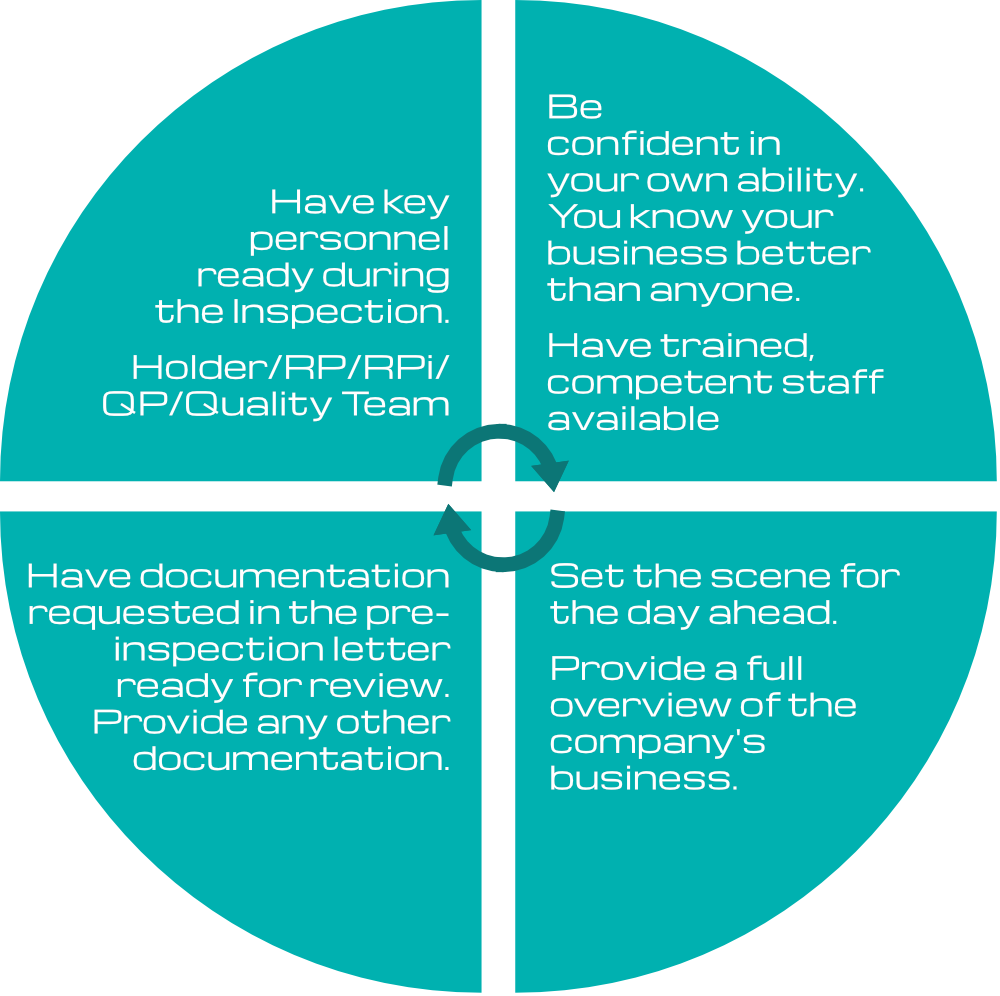
Interpreting what the MHRA inspector requires is not always an easy task. For example, what the pharmaceutical professional sees as suitable may not always correspond with what the inspector sees as suitable. This can often be confusing and daunting, particularly when a significant amount of work has already been put into writing and implementing the QMS, training and other key quality processes.
Interpreting questions and what the expected answer should be can sometimes be confusing. If there is ambiguity, ask the inspector to clarify the question, or ask them to explain it differently. This is very important, and indeed, you must ask for clarification if you do not fully understand what the inspector is requesting.
- Be honest and open
- Show what the risks are to your supply chain
- What current control measures are in place?
- Define processes and procedures in the quality management system
- Ensure staff are fully trained (ongoing) and competency training conducted
The inspector is attending to ensure you are complying with your regulatory obligation in protecting patient safety and ensuring product quality is maintained throughout the supply chain. Remember they are not there to advise or recommend.
Both the RP and the inspector have a common purpose and that is to protect patient safety and maintain product quality.
What not to ask an inspector
Am I doing it right?
Can you advise me?
Is there sufficient/adequate information in my procedures?
The inspector needs to feel confident that you understand your business model and can demonstrate your understanding of the regulations and GDP is carried out effectively. You will be expected to know you have identified, accessed, mitigated, and communicated risks. Demonstrating RP full oversight, understanding and control is fundamental in providing the inspector with assurances these obligations are being fulfilled.
What did I see as an inspector?
As an inspector, I was often incredibly impressed by the hard work and commitment of RPs, licence holders and their teams. However, all too often, companies can get bogged down in the desire to create systems that can be over-complicated. This includes producing risk assessments that fail to consider causal factors, written procedures that did not reflect the business model or work instructions that didn’t link to the correct procedure. Creating complex systems can be challenging to implement and difficult for staff to be engaged with, particularly when faced with operational factors that can impact on the day job, such as system failures, vehicle breakdown, inclement weather, shortages of medicines, increased stock holding, staff shortages etc etc.
Many RPs are extremely conscientious and want to ensure patient safety and product quality is at the forefront of the business ethos and strive in their role to ensure compliance is controlled and maintained and staff have a thorough understanding of their own roles. Having processes and systems that are overly complex can sometimes be more detrimental to providing assurances to the regulator that complete control is in place and that staff fully understand what is expected of them. Failure to recognise this could have an impact on the organisation’s outcome of an inspection.
So how can you simplify things?
Take a step back and ask yourself, what skillset do we have in our organisation? What benefits can we draw from identifying other areas of expertise in our existing team? For example, when I first became an inspector with the MHRA, I was also qualified in Health & Safety. The skills acquired in my previous employment allowed me to understand risk management and its underlying principles. This provided me with the opportunity to use this knowledge in my role as an inspector, albeit there were other areas of being an inspector where I had to undergo a significant amount of training.
One of the first things to do is identify what technical knowledge your staff have. Overlooking fundamental skillsets in your own organisation may mean your greatest asset is sitting right there and you are unaware!
Ask staff what they think. Is this operating procedure too ambiguous? Are we doing what the work instruction tells us to do? Can we use pictorial training methods alongside written processes? Are we working efficiently and effectively? As an RP, have you considered bouncing ideas off other RPs who you might have met during training?
Knowledge is gained in several ways.
School, college, university, carrying out your daily role, training sessions, listening to webinars, attending seminars. We often overlook the type of training we attend and forget to record it or, when we attend such events, we forget to disseminate it to those who would benefit within the business. Information sharing is vital not only to promoting and safeguarding medicinal product, but it also empowers and increases team morale and provides colleagues with a sense of responsibility.
From regulatory inspector to director
The transition from an MHRA regulatory inspector to a Director of SeerPharmaUK and a trainer in the training team is providing me with the opportunity to work in an environment with skilled and talented individuals who share the same passion – helping those who want to get it right and sharing the wealth of knowledge from 25 years working in industry and as a senior regulatory inspector.
Ask advice of people who know
SeerPharmaUK can provide guidance, encouragement and training. We can harness your existing knowledge, develop it to maximise your understanding of regulatory requirements and provide guidance on the expectations of the inspector. Simply having a chat sometimes helps to sort out ambiguity.
Trainers/consultants can provide a useful distance from the challenges of your business; they are not emotionally invested in operations in the same way that business owners are, and they can more easily identify and address challenges, whether the issue is implementing a new quality system or clarifying regulatory requirements.
A consultation with us can afford the freedom to bring knowledge and experience to the table, to be impartial yet observational (a fresh pair of eyes), have an open discussion on perhaps some of the weaker areas of the business and identify the stronger areas.
Sharing information through training is fundamental to all stakeholders. Many companies want to get it right and many do. However, some need that extra advice, guidance, training, and a suitable strategy to gain the recognition they so clearly deserve.
Remember, the inspector wants the same as you; both of you are working towards the same outcome.
The SeerPharma UK Team – What makes us different?
The diversity of the directors in the SeerPharmaUK team is unique. My SeerPharmaUK colleagues and I have met a lot of people through our interactions and networking.
We have an extensive pool of skills with a breadth of experience in industry, regulatory, training and consultancy and we can help support you.
We have had the unique opportunity of seeing this from both sides of the fence, which has been enlightening, interesting and insightful. We see some very high industry standards, but we also see a lot of RPs working in isolation- something I often didn’t see as an inspector. When working in isolation, it can be difficult to assess if you’re on the right track or fully complying with your duties, wanting to get it right, but not confidently knowing if you are. We have the knowledge & skillset at our fingertips and can provide the help and guidance to confirm you are on the right path. Considering my own industry experience, I wish there had been an organisation such as SeerPharmaUK out there to help us.
Do I feel like gamekeeper turned poacher? No I don’t. I believe we can all work together to achieve the same outcome and good training, guidance and an ear to listen can make all the difference.
So, in anticipating an inspection, preparation is key. Taking time to consider what training may be required well before the MHRA letter drops through the door, will lessen the impact, and make the inspection a more relaxed experience. The SeerPharmaUK team are here to help you.
If you would like a chat, please contact us.
Sign up for our regular communications
It’s all here, from must-read articles, savings on training to being the first to know about new courses… of course you need to know!